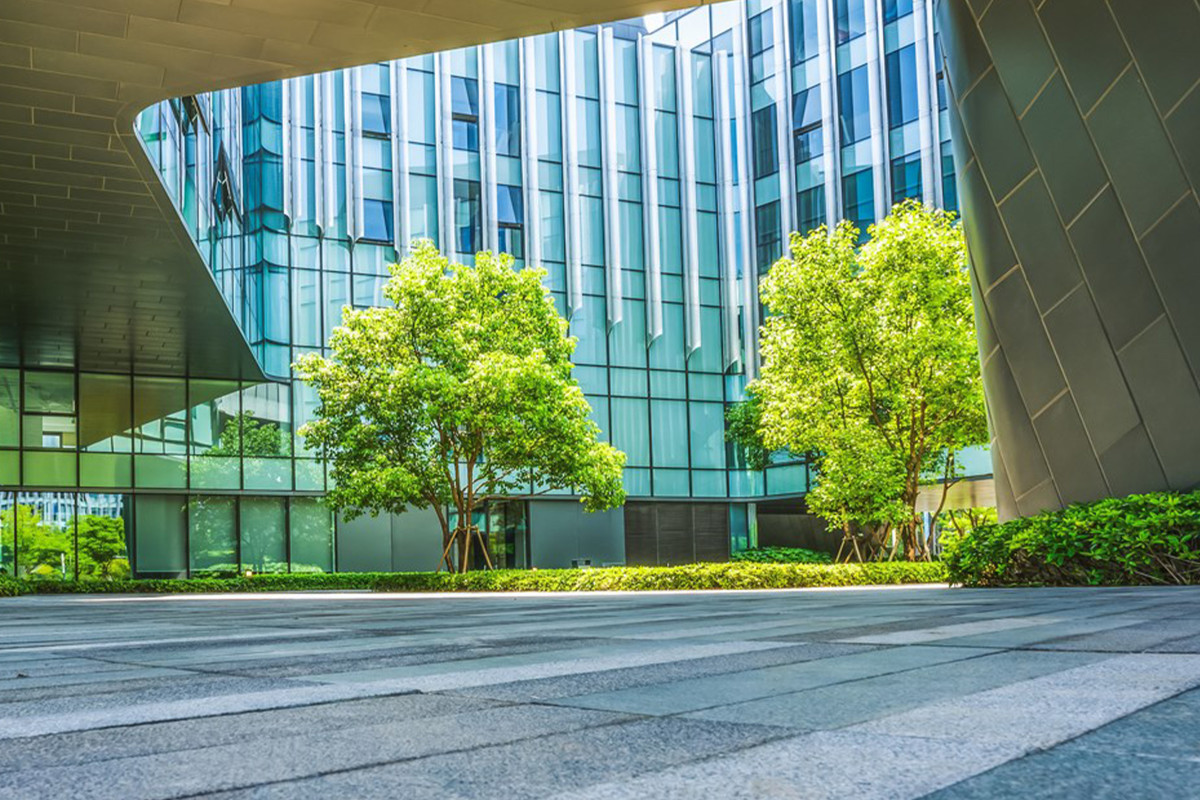
Corporate Social Responsibility
Behaving responsibly as a global citizen is an inextricable part of our heritage, and we uphold the highest ideals of integrity, innovation and excellence in all we do. We turn investments in innovation into technology and services that help our customers be more productive, profitable and sustainable. We do this with the same core values our founder established decades ago. Learn more about how we conduct business ethically and in an environmentally and socially conscious manner to help our customers, empower our people, and protect our planet.
Corporate Social Responsibility Report
CSR Annual ReportProgress Summary
Materiality at Xerox
Xerox assesses corporate social responsibility topics that are important to our stakeholders and those where we can have the greatest economic, social, and environmental impact at local, regional, and global levels. We update our materiality assessment every two to three years on average. In 2023, Xerox engaged a third party to lead us through a double materiality impact assessment See detailed information about the process, the list of material topics and key insights and observations.
How We Report
GRI Index
See how Xerox aligns with the GRI Standards framework set forth by the Global Reporting Initiative (GRI).
SASB Report
See how Xerox addresses key areas defined by Sustainability Accounting Standards Board (SASB) Sustainable Industry Classification System™.
TCFD Report
See our Task Force on Climate Change Disclosures.
At A Glance
2040
New goal year for achieving net zero emissions
200%
Increase of employee donations from 2020 to 2021
100%
New, eligible products registered with Energy Star® and EPEAT
10
Employee Resource Groups
40%
Board diversity
240M
Pounds of carbon dioxide offset through PrintReleaf
Recognition
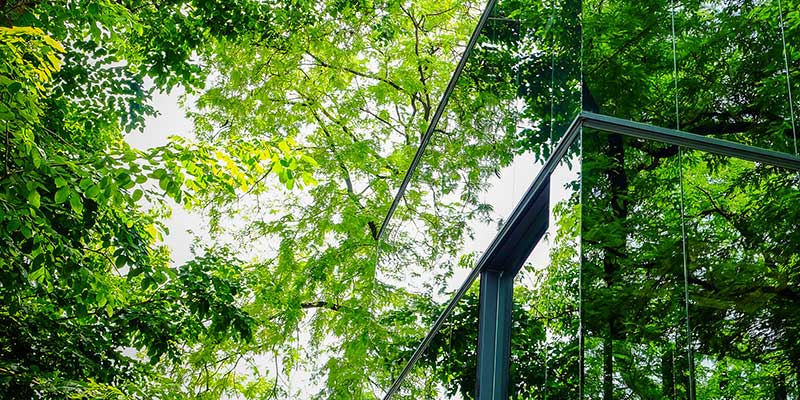
Corporate Knights' List of Most Sustainable Corporations
Corporate Knights recognized Xerox among most sustainable corporations. Learn more about why our sustainability goals and net-zero roadmap put Xerox ahead of nearly 7,000 other companies on the list.
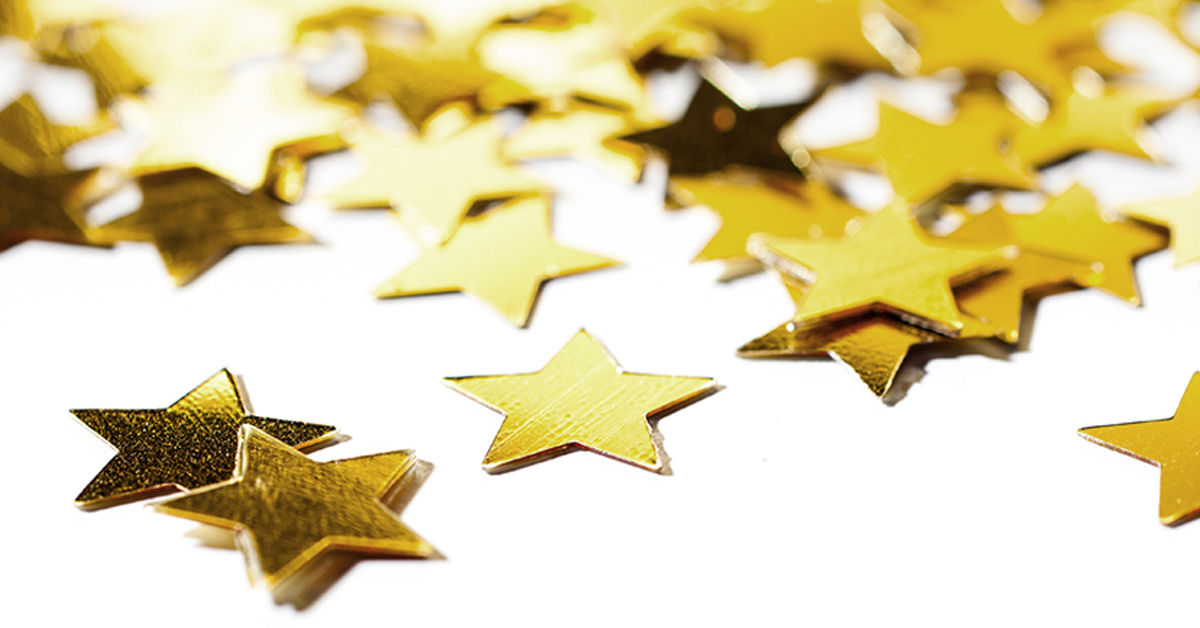
Xerox Receives ENERGY STAR®’s Highest Honor
Xerox, with a legacy of innovation that helps make the world a more sustainable place, is honored to have received the 2024 ENERGY STAR® Partner of the Year Award.
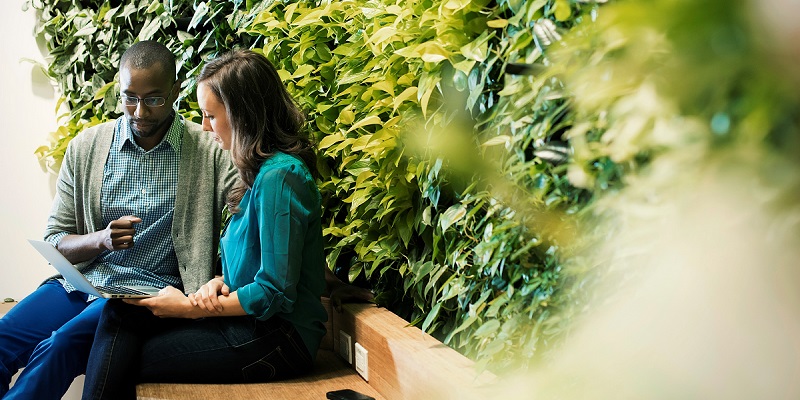
Xerox Named a Sustainability Leader in the Print Industry by Quocirca
Quocirca, a leading source for independent research, thought leadership, and actionable insight for the print industry, has named Xerox a sustainability leader in its Sustainability Trends 2023 report.

Xerox Named One of America’s Most Responsible Companies by Newsweek
Xerox is featured among the top 500 largest public companies in the U.S. for the fourth consecutive year.
Diversity, Inclusion & Belonging
Making this a better planet for everyone for more than 50 years.
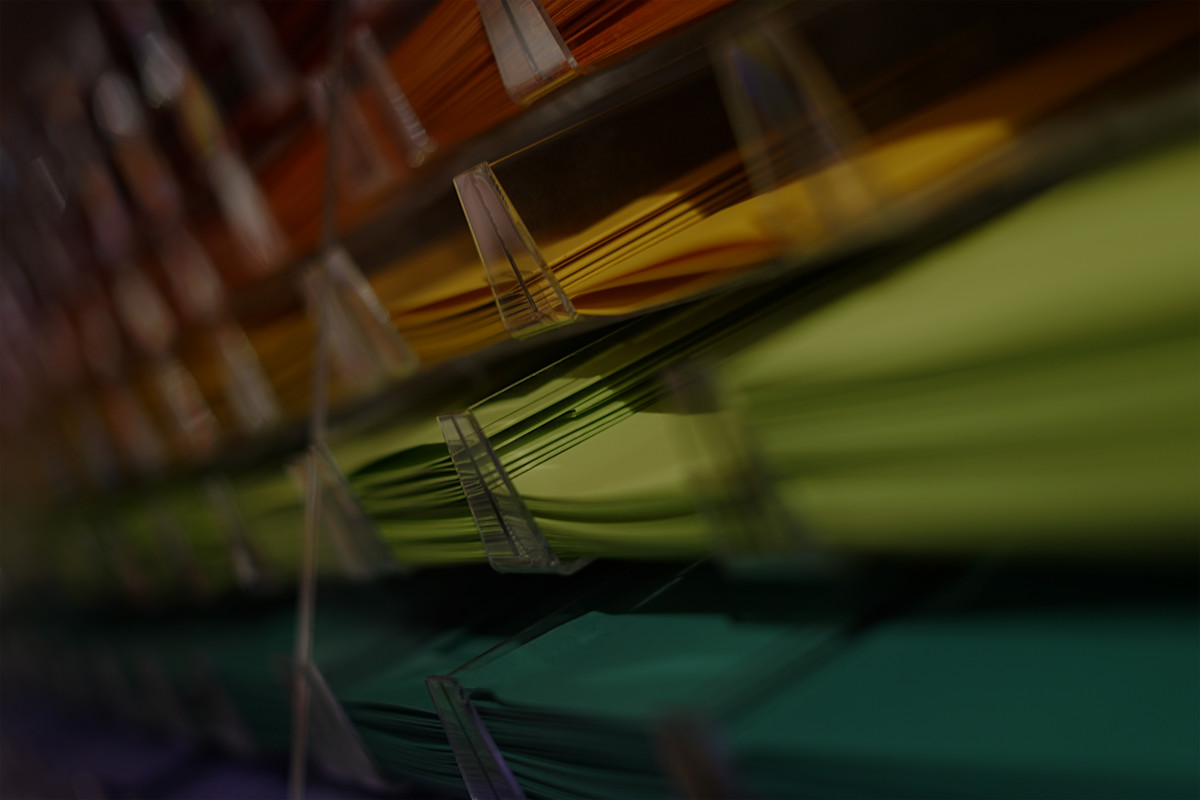
Our Commitments
We fully embrace our social and environmental responsibilities, and we are committed to conducting business in ways that positively impact the world.
Governance
Governance
Environment
Environment
Society
Society