
Innovation at Xerox
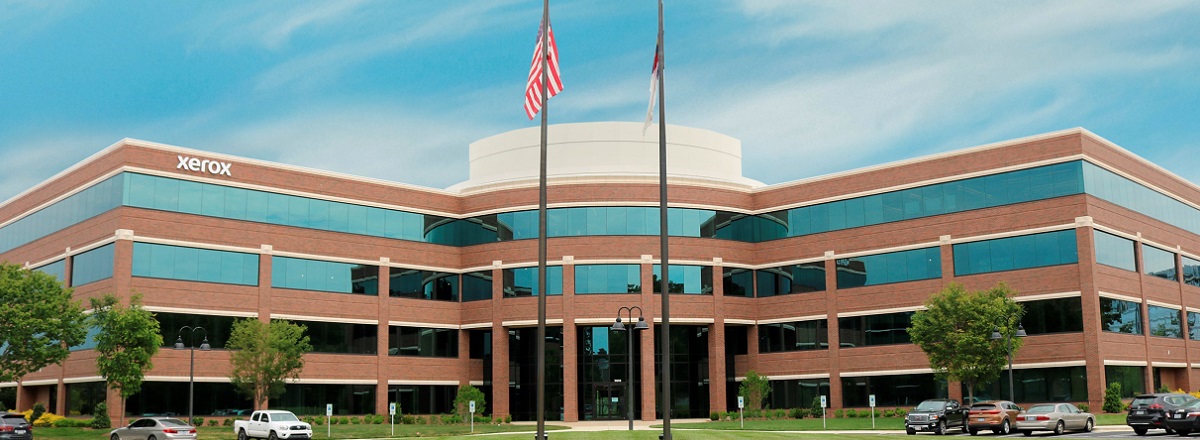
North Carolina Center of Excellence
Xerox’s North Carolina Center of Excellence utilizes the latest technologies for a collaborative environment that fosters innovation. Customers can experience new technologies from Xerox here, including our 3D printing lab.
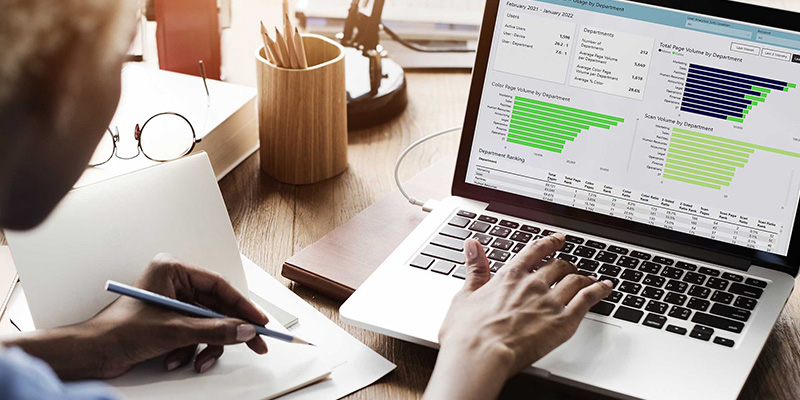
Microanalytical insight
Using the latest analytical instrumentation, our analysts provide critical insight to characterize materials.
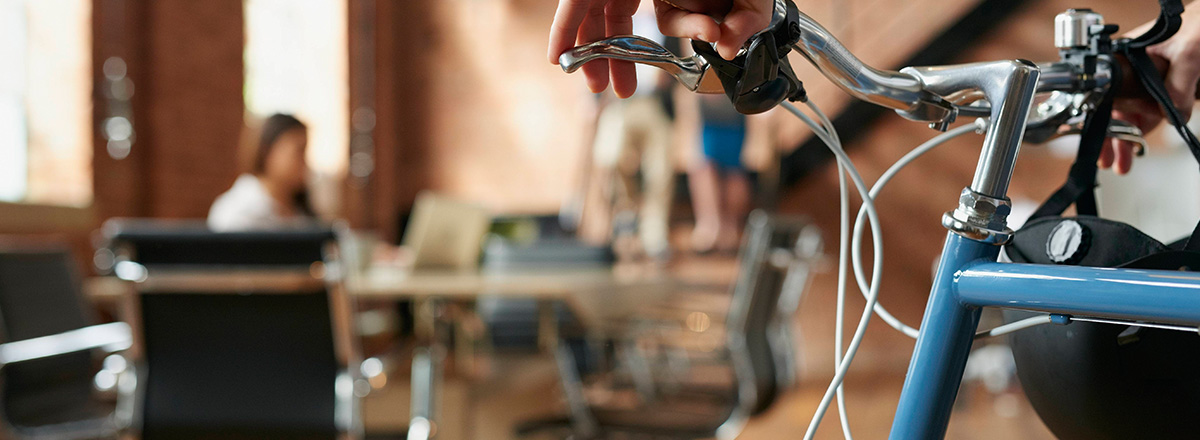
Sustainable Technology
We turn innovation investments into products and services that help our customers be more productive, profitable and sustainable.
Xerox has a proud history of pioneering research, and continues to be in the forefront of innovation.

Innovation Insights
Find more articles about what is happening in our labs and the work of some of the brightest minds on the planet.

Search for Xerox Jobs
Join a team that thrives on new thinking and finding new ways to solve the latest challenges our customers face.